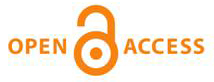
Address: Naberezhnaya Severnoy Dviny, 17, Arkhangelsk, 163002, Russian Federation, Northern (Arctic) Federal University named after M.V.Lomonosov, office 1425
Phone: +7 (8182) 21-61-18
E-mail: forest@narfu.ru
http://lesnoizhurnal.ru/en/
|
Specific Energy Costs of Grinding Wood when Preparing a Composite for 3D-Printing. P. 159–176
|
 |
Nikolay P. Midukov, Nikolay V. Evdokimov, Victor S. Kurov, Valerii V. Korshunov
UDС
678.046.52
DOI:
10.37482/0536-1036-2024-4-159-176
Abstract
The Northwestern Federal District is a region of Russia rich in a variety of wood species. The properties of wood in this region differ significantly from the properties of wood grown in other countries or in the eastern part of Russia, which leads to differences in energy costs of grinding wood. The aim of this research has been to estimate the specific energy costs of grinding wood to the state of wood flour, which will be used as the basis for wood polymer composite consumables in additive technologies. Wood flour has been obtained by grinding wood in a laboratory disk mill, repeatedly reducing the particle size. The granulometric composition has been analyzed for beech, oak, larch, alder and pine wood at 1, 3, 5 and 10 grinding cycles. Particle sizes have been determined by analyzing images obtained using an optical microscope and processed in the ImageJ graphic program. The specific energy costs of grinding have been estimated by recording the power with a wattmeter every second with repeated feeding of wood flour for the known mill productivity. When calculating the specific energy consumption, the moisture content of each wood species has been taken into account, as well as productivity losses associated with the adhesion of wood particles to the working surfaces of the dispersing set and the inner area of the disk mill body. The research has revealed a relationship between the specific energy costs and the particle size of wood flour obtained from various wood species. Regression analysis of curves corresponding to different wood species has made it possible to obtain exponential and power-law dependencies that do not contradict the fundamental theoretical laws of grinding solid particles. Based on these results, pine wood flour has been recognized as the most energy-efficient option. The established dependencies can be used to predict the specific energy consumption for grinding beech, oak, larch, alder and pine wood in disk mills.
Affiliation
1Saint-Petersburg State University of Industrial Technologies and Design, ul. Ivana Chernykh, 4, Saint Petersburg, 198095, Russian Federation; mnp83@mail.ru*, nikoev@rambler.ru,
vskurov18@mail.ru
2LLC “DrobTechMash”, ul. Tsentral’naya, 57, of. 337, Ufa, 450024, Russian Federation; korshunof@bk.ru
Keywordswood flour, wood-polymer composite, wood grinding, specific energy costs, particle size distribution
For citation
Midukov N.P., Evdokimov N.V., Kurov V.S., Korshunov V.V. Specific Energy Costs of Grinding Wood when Preparing a Composite for 3D-Printing. Lesnoy Zhurnal = Russian Forestry Journal, 2024, no. 4, pp. 159–176. (In Russ.). https://doi.org/10.37482/0536-1036-2024-4-159-176
References
-
Alashkevich Yu.D., Yurtaeva L.V., Reshetova N.S., Marchenko R.A. The Influence of the Knife Method of Grinding Pulp on the Process of Obtaining Powdered Cellulose. Khimiya Rastitel’nogo Syr’ya, 2020, no. 4, pp. 493–499. (In Russ.). https://doi.org/10.14258/jcprm.2020048121
-
Borisov N.A. Production of Finely Ground Wood Flour. Moscow, 1964. 21 p. (In Russ.).
-
Gauze A.A., Goncharov V.N. Fundamentals of Theory and Calculation of Equipment for Preparing Paper Pulp. St. Petersburg, 2017, part 1. 84 p. (In Russ.).
-
Klesov A.A. Wood-Polymer Composites. St. Petersburg, Nauchnye osnovy i tekhnologii Publ., 2010. 735 p. (In Russ.).
-
Leonovich A.A. Physico-Chemical Basis for the Formation of Wood Boards. St. Petersburg, Khimizdat Publ., 2003. 192 p. (In Russ.).
-
Leonovich A.A. Wood-Based Panel Technology: Progressive Solutions. St. Petersburg, Khimizdat Publ., 2005. 206 p. (In Russ.).
-
Leonovich A.A. New Wood-Based Materials. St. Petersburg, Khimizdat Publ., 2008. 158 p. (In Russ.).
-
Lipilin A.B., Vexler M.V., Korenyugina N.V., Morozov A.M., Kononov G.N., Kosarev K.L., Kudryashov A.V. Thin Grinding and Drying of Timber in Vortex Mill-Heater. Lesnoy Vestnik = Forestry Bulletin, 2013, no. 3, pp. 139–144. (In Russ.).
-
Midukov N.P., Kurov V.S., Evdokimov N.V. Biorefining of Wood-Fibre Raw Material in a Material Composition for Additive Technologies. Khimicheskie volokna = Fibre Chemistry, 2023, vol. 55, no. 1, pp. 53–58. (In Russ.). https://doi.org/10.1007/s10692-023-10426-6
-
Morozov A.M., Kononov G.N., Kosarev K.L., Kudryashov A.V. Using of Scanning Electron Microscopy to Studying Nanoporous Structure Products of Timber Processing. Lesnoy Vestnik = Forestry Bulletin, 2013, no. 2, pp. 72–76. (In Russ.).
-
Politov A.A., Bershak O.V., Lomovskij O.I. Method for Production of Wood Flour. Patent RF, no. RU 2318655 C1, 2008. (In Russ.).
-
Sidenko P.M. Grinding in the Chemical Industry: 2nd ed., revised. Moscow, Khimiya Publ., 1977. 368 p. (In Russ.).
-
Spiglazov A.V., Stavrov V.P. The Influence of the Size of Wood Particles and the Degree of Filling on the Fluidity of Compositions with Polypropylene. Plasticheskie massy, 2004, no. 12, pp. 50–52. (In Russ.).
-
Khint I.A., Kuz’minov V.A. Production of Silicalcite and its Use in Housing Construction. Tallin, 1958. 216 p. (In Russ.).
-
Tsyvin M.M., Kottsov S.G., Shmakhov I.V. Wood Flour Production. Moscow, Lesnaya promyshlennost’ Publ., 1982. 134 p. (In Russ.).
-
Chistova N.G., Matygulina V.N., Alashkevich Yu.D. Preparation of Wood-Fiber SemiFinished Products in Knife Machines of Various Modification. Khimiya Rastitel’nogo Syr’ya, 2020, no. 4, pp. 459–466. (In Russ.). https://doi.org/10.14258/jcprm.2020048189
-
Aliev S.S., Egamberdiev E.A., Akmalova G.Yu., Ilkhamov G.Yu. Analysis of Physical-Mechanical Properties of New Type of Wood-Polymer Composite Materials. Harvard Educational and Scientific Review, 2023, vol. 3, iss. 1, pp. 48–53.
-
Delviawan A., Kojima Y., Kobori H., Suzuki S., Aoki K., Ogoe S. The Effect of Wood Particle Size Distribution on the Mechanical Properties of Wood–Plastic Composite. Journal of Wood Science, 2019, vol. 65, art. no. 67. https://doi.org/10.1186/s10086-019-1846-9
-
Karinkanta P., Ämmälä A., Illikainen M., Niinimäki J. Fine Grinding of Wood – Overview from Wood Breakage to Applications. Biomass and Bioenergy, 2018, vol. 113, pp. 31–44. https://doi.org/10.1016/j.biombioe.2018.03.007
-
Pokhrel G., Gardner D.J., Han Y. Properties of Wood–Plastic Composites Manufactured from Two Different Wood Feedstocks: Wood Flour and Wood Pellets. Polymers, 2021, vol. 13, no. 16, art. no. 2769. https://doi.org/10.3390/polym13162769
-
Pokhrel G., Han Y., Gardner D.J. Comparative Study of the Properties of Wood Flour and Wood Pellets Manufactured from Secondary Processing Mill Residues. Polymers, 2021, vol. 13, no. 15, art. no. 2487. https://doi.org/10.3390/polym13152487
-
Pušnik Črešnar K., Fras Zemljič L., Slemenik Perše L., Bek M. Effect of Wood Fiber Loading on the Chemical and Thermo-Rheological Properties of Unrecycled and Recycled Wood-Polymer Composites. Applied Sciences, 2020, vol. 10, no. 24, art. no. 8863. https://doi.org/10.3390/app10248863
-
Rajaonariony K.R., Mayer-Laigle C., Piriou B., Rouau X. Comparative Comminution Efficiencies of Rotary, Stirred and Vibrating Ball-Mills for the Production of Ultrafine Biomass Powders. Energy, 2021, vol. 227, art. no. 120508. https://doi.org/10.1016/j.energy.2021.120508
-
Sturges H.A. The Choice of a Class Interval. Journal of the American Statistical Association, 1926, vol. 21, iss. 153, pp. 65–66. https://doi.org/10.1080/01621459.1926.10502161
-
Wang J., Gao J., Brandt K.L., Wolcott M.P. Energy Consumption of Two-Stage Fine Grinding of Douglas-Fir Wood. Journal of Wood Science, 2018, vol. 64, pp. 338–346. https://doi.org/10.1007/s10086-018-1712-1
Specific Energy Costs of Grinding Wood when Preparing a Composite for 3D-Printing. P. 159–176
|
Make a Submission
Lesnoy Zhurnal (Russian Forestry Journal) was awarded the "Seal of Recognition for Active Data Provider of the Year 2025"
|