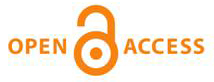
Address: Naberezhnaya Severnoy Dviny, 17, Arkhangelsk, 163002, Russian Federation, Northern (Arctic) Federal University named after M.V.Lomonosov, office 1425
Phone: +7 (8182) 21-61-18
E-mail: forest@narfu.ru
http://lesnoizhurnal.ru/en/
|
Performance Characteristics of Wood-Polymer Composites Based on Acetylated Wood Filler. P. 147–158
|
 |
Anatoliy А. Prokopiev, Nour R. Galyavetdinov, Ruslan R. Safin
UDС
691.11
DOI:
10.37482/0536-1036-2024-4-147-158
Abstract
The demand for composite materials is growing every year. In this regard, the competitiveness of a particular product is determined primarily by the price-quality ratio. The most rational option for the production of wood-filled composites is using the materials with the increased performance characteristics. To date, it is the performance characteristics of modern composite materials that are the most significant, not only for final consumers, but also for manufacturers. In this regard, to improve performance characteristics in the production of wood-filled composites, various methods of pre-treatment of wood are used – thermal modification, acetylation, furfulation, ultra-high-frequency processing, alkali treatment, the use of various additives, etc. A promising way to improve the physical and mechanical properties of wood-filled materials is acetylation, whose mechanism consists in the formation of acetyl groups in wood during processing. To reduce production costs and the cost of the final product, it is possible to use a cheaper precursor (for example, icy acetic acid instead of acetic anhydride) with the possibility of intensifying the impregnation process. This article presents the results of obtaining wood-filled composites based on acetylated birch wood flour with its various proportions in the composition. The effect of introducing acetylated wood filler into the composition on the performance properties of composites (abradability, frost-resistance, flexural strength) has been evaluated in comparison with control samples made from untreated birch wood flour. The effect of acetylation with glacial acetic acid on the structure of birch wood flour has been characterized using Fourier-transform infrared spectroscopy. The IR-spectra of the control and acetylated samples contain absorption bands belonging to the corresponding groups of cellulose and lignin of hardwoods. The abradability and frost-resistance coefficients for a wood-filled composite based on acetylated birch wood flour are on average 1.5–2 times lower for all compositions compared to control samples. The results of the research allow us to conclude that acetylation of wood flour as a method of pre-treatment of the filler in order to improve the performance characteristics of the final product is promising for implementation in the production of wood-filled materials.
Keywordswood flour, acetylation, glacial acetic acid, wood-filled composite, IR-Fourier spectroscopy, ultimate flexural strength, abradability, frost-resistance
For citation
Prokopiev A.A., Galyavetdinov N.R., Safin R.R. Performance Characteristics of Wood-Polymer Composites Based on Acetylated Wood Filler. Lesnoy Zhurnal = Russian Forestry Journal, 2024, no. 4, pp. 147–158. (In Russ.). https://doi.org/10.37482/0536-1036-2024-4-147-158
References
-
Pozhidaev V.M., Retivov V.M., Panarina E.I., Sergeeva Ya.E., Zhdanovich O.A., Yatsishina E.B. Development of a Method for Identifying Wood Species in Archaeological Materials by IR Spectroscopy. Zhurnal analiticheskoj khimii = Journal of Analytical Chemistry, 2019, vol. 74, no. 12, pp. 911–921. (In Russ.). https://doi.org/10.1134/S0044450219120107
-
Prokopiev A.A., Salimgaraeva R.V., Safin R.R. Review of Modern Research in the Field of Wood Acetylation. Derevoobrabativaushaya promishlennost’ = Woodworking Industry, 2022, no. 2, pp. 106–114. (In Russ.).
-
Prokopiev A.A., Salimgaraeva R.V., Safin R.R. Investigation of the Properties of Acetylated Wood. Derevoobrabativaushaya promishlennost’ = Woodworking Industry, 2023, no. 1, pp. 86–91. (In Russ.).
-
Prokopiev A.A., Salimgaraeva R.V., Safin R.R. Investigation of the Properties of Wood-Polymer Composites Based on Acetylated Wood Filler. Sistemy. Metody. Tekhnologii = Systems. Methods. Technologies, 2023, no. 2(58), pp. 99–106. (In Russ.). https://doi.org/10.18324/2077-5415-2023-2-99-106
-
Alfredsen G., Pilgård A. Postia placenta Decay of Acetic Anhydride Modified Wood – Effect of Leaching. Wood Material Science & Engineering, 2014, vol. 9, iss. 3, pp. 162–169. https://doi.org/10.1080/17480272.2014.887776
-
Bongers F., Meijerink T., Lütkemeier B., Lankveld C., Alexander J., Militz H., Lehringer C. Bonding of Acetylated Wood. International Wood Products Journal, 2016, vol. 7, iss. 2, pp. 102–106. https://doi.org/10.1080/20426445.2016.1161944
-
Borysiak S., Paukszta D. Mechanical Properties of Lignocellulosic / Polypropylene Composites. Molecular Crystals and Liquid Crystals, 2008, vol. 484, no. 1, pp. 13/379 – 22/388. https://doi.org/10.1080/15421400801901464
-
Çetin N.S., Özmen N., Birinci E. Acetylation of Wood with Various Catalysts. Journal of Wood Chemistry and Technology, 2011, vol. 31, iss. 2, pp.142–153. https://doi.org/10.1080/02773813.2010.503981
-
Eranna P.B., Pandey K.K., Nagarajappa G.B. A Note on the Effect of Microwave Heating on Iodine-Catalyzed Acetylation of Wood. Journal of Wood Chemistry and Technology, 2016, vol. 36, iss. 3, pp. 205–210. https://doi.org/10.1080/02773813.2015.1112405
-
Fodor F., Németh R., Lankveld C., Hofmann T. Effect of Acetylation on the Chemical Composition of Hornbeam (Carpinus betulus L.) in Relation with the Physical and Mechanical Properties. Wood Material Science & Engineering, 2018, vol. 13, iss. 5, pp. 271–278. https://doi.org/10.1080/17480272.2017.1316773
-
Hamid N.H., Hale M. Decay Threshold of Acetylated Rattan against White and Brown Rot Fungi. International Wood Products Journal, 2012, vol. 3, iss. 2, pp. 96–106. https://doi.org/10.1179/2042645311Y.0000000018
-
Joeressen J., Baumann G., Spirk S., Krenke T., Schönauer T., Feist F. Chemical Resistance of Acetylated Radiata Pine Sliced Veneers. Wood Material Science & Engineering, 2022, vol. 18, iss. 4, pp. 1467–1477. https://doi.org/10.1080/17480272.2022.2155565
-
Khoaele K.K., Gbadeyan O.J., Chunilall V., Sithole B. A Review on Waste Wood Reinforced Polymer Composites and Their Processing for Construction Materials. International Journal of Sustainable Engineering, 2023, vol. 16, iss. 1, pp. 104–116. https://doi.org/10.1080/19397038.2023.2214162
-
Li J.-Z., Furuno T., Zhou W.-R., Ren Q., Han X.-Z., Zhao J.-P. Properties of Acetylated Wood Prepared at Low Temperature in the Presence of Catalysts. Journal of Wood Chemistry and Technology, 2009, vol. 29, iss. 3, pp. 241–250. https://doi.org/10.1080/02773810903009499
-
Marsich L., Cozzarini L., Ferluga A., Solinas D., Schmid C. The Effect of Acetylation on Hybrid Poplar after Artificial Weathering. International Wood Products Journal, 2018, vol. 9, iss. 3, pp. 134–141. https://doi.org/10.1080/20426445.2018.1513893
-
Pizzi A., Zhou X., Navarrete P., Segovia C., Mansouri H.R., Placentia Pena M.I., Pichelin F. Enhancing Water Resistance of Welded Dowel Wood Joints by Acetylated Lignin. Journal of Adhesion Science and Technology, 2013, vol. 27, iss. 3, pp. 252–262. https://doi.org/10.1080/01694243.2012.705512
-
Popescu C.M., Hill C.A.S., Popescu M.C. Water Adsorption in Acetylated Birch Wood Evaluated through Near Infrared Spectroscopy. International Wood Products Journal, 2016, vol. 7, iss. 2, pp. 61–65. https://doi.org/10.1080/20426445.2016.1160538
-
Rowell R.M. Acetylation of Natural Fibers to Improve Performance. Molecular Crystals and Liquid Crystals, 2004, vol. 418, iss. 1, pp. 153–164. https://doi.org/10.1080/15421400490479244
-
Rowell R.M. Chemical Modification of Wood: A Short Review. Wood Material Science & Engineering, 2006, vol. 1, iss. 1, pp. 29–33. https://doi.org/10.1080/17480270600670923
-
Rowell R.M., Ibach R.E., McSweeny J., Nilsson T. Understanding Decay Resistance, Dimensional Stability and Strength Changes in Heat-Treated and Acetylated Wood. Wood Material Science & Engineering, 2009, vol. 4, iss. 1–2, pp. 14–22. https://doi.org/10.1080/17480270903261339
-
Rozman H.D., Kumar R.N., Khalil H.P.S.A., Abusamah A., Abu R. Chemical Modification of Wood with Maleic Anhydride and Subsequent Copolymerization with Diallyl Phthalate. Journal of Wood Chemistry and Technology, 1997, vol. 17, iss. 4, pp. 419–433. https://doi.org/10.1080/02773819708003142
-
Sethy A.K., Vinden P., Torgovnikov G., Militz H., Mai C., Kloeser L., Przewloka S. Catalytic Acetylation of Pinus radiata (D. Don) with Limited Supply of Acetic Anhydride Using Conventional and Microwave Heating. Journal of Wood Chemistry and Technology, 2012, vol. 32, iss. 1, pp. 1–11. https://doi.org/10.1080/02773813.2011.573121
-
Wålinder M., Brelid P.L., Segerholm K., Long C.J., Dickerson J.P. Wettability of Acetylated Southern Yellow Pine. International Wood Products Journal, 2013, vol. 4, iss. 3, pp. 197–203. https://doi.org/10.1179/2042645313Y.0000000045
-
Zelinka S.L., Passarini L. Corrosion of Metal Fasteners Embedded in Acetylated and Untreated Wood at Different Moisture Contents. Wood Material Science & Engineering, 2018, vol. 15, iss. 4, pp. 182–189. https://doi.org/10.1080/17480272.2018.1544171
Performance Characteristics of Wood-Polymer Composites Based on Acetylated Wood Filler. P. 147–158
|
Make a Submission
Lesnoy Zhurnal (Russian Forestry Journal) was awarded the "Seal of Recognition for Active Data Provider of the Year 2025"
|