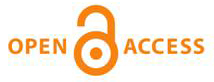
Address: Naberezhnaya Severnoy Dviny, 17, Arkhangelsk, 163002, Russian Federation, Northern (Arctic) Federal University named after M.V.Lomonosov, office 1425
Phone: +7 (8182) 21-61-18
E-mail: forest@narfu.ru
http://lesnoizhurnal.ru/en/
|
Changes in the Morphological Characteristics of Secondary Fiber Obtained from Wet-Strength Paper During Gentle Refining of the Recycled Pulp. Part 2. Fines Characteristics. P. 169–179
|
 |
Penkin A.A., Kazakov Y.V.
UDС
676.038:676.017.44
DOI:
10.37482/0536-1036-2023-4-169-179
Abstract
The process of recycled pulp refining is usually associated with a significant change in the morphological characteristics of the secondary fiber and the formation of additional amounts of fines. It is well known that fines have a great impact on the pulp properties, the papermaking process and the quality of the resulting paper. At the same time, the effect of fines both on the paper properties and on the papermaking process depends on the morphological characteristics of the fines. The aim of the study was to evaluate the changes in the morphological characteristics of the fines during gentle low-consistency refining of the recycled pulp. The recycled pulp was obtained from commercial wet-strength tissue paper, consisting of 100 % bleached softwood kraft pulp (BSKP) made from pine (Pinus sylvestris L.). The repulping of wet-strength paper was performed at 60 °C in three ways, namely, repulping with sodium hydroxide (indicated as RP (NaOH)), repulping with sodium hydroxide and sodium persulfate (RP (NaOH + Na2S2O8)), and finally repulping with sodium hydroxide and potassium monopersulfate (RP (NaOH + KHSO5)). Using an optical fiber analyzer, L&W Fiber Tester, it was found that accelerated persulfate and monopersulfate repulping of the wet-strength paper led to an increase in fines content after pulp refining by 0.20…0.28 % on length and by 0.9…1.5 % on number of particles. In addition, some fines were not detected due to the limited resolution of the measuring device. The morphological characteristics of the recycled pulps showed that the studied fines were relatively straight particles (Sl = 93.5...94.0 %) with low length polydispersity ((Ll/Ln) = 1.08...1.09). Fines had a mean slenderness ratio (L/W)l and (L/W)w of about 7, which in some length classes reached 8...9. Taking into account the experimental data on fines length (Ll = 132…134 µm) and fiber width (Wl = 29.7…30.0 µm), as well as SEM images of recycled paper, we can conclude that these particles can form fines-assisted bridges between several close deposited fibers in the fiber network, thus strengthening the paper web.
Affiliation
1Belarusian State Technological University, ul. Sverdlova, 13a, Minsk, 220006, Republic of Belarus; penkin@belstu.by*
2Northern (Arctic) Federal University named after M.V. Lomonosov, Naberezhnaya Severnoy Dviny, 17, Arkhangelsk, 163002, Russian Federation; j.kazakov@narfu.ru
Keywordswet-strength paper, repulping, recycled pulp, gentle refining, fines, morphological characteristics
For citation
Penkin A.A., Kazakov Y.V. Changes in the Morphological Characteristics of Secondary Fiber Obtained from Wet-Strength Paper During Gentle Refining of the Recycled Pulp. Part 2. Fines Characteristics. Lesnoy Zhurnal = Russian Forestry Journal, 2023, no. 4, pp. 169–179. (In Russ.). https://doi.org/10.37482/0536-1036-2023-4-169-179
References
-
Kazakov Y.V. The Characteristic of Geometrical Parameters of Cellulose Fibers in Pulp Using Probabilistic Approach. Khimija Rastitel’nogo Syr’ja = Chemistry of Plant Raw Material, 2014, no. 1, pp. 269–275. (In Russ.). https://doi.org/10.14258/jcprm.1401269
-
Penkin A.A., Kazakov Y.V. Changes in the Morphological Characteristics of Secondary Fiber Obtained from Wet-Strength Paper During Gentle Refining of the Recycled Pulp. Part 1: Fiber Characteristics. Lesnoy Zhurnal = Russian Forestry Journal, 2022, no. 5, pp. 157–172. (In Russ.). https://doi.org/10.37482/0536-1036-2022-5-157-172
-
Smolin A.S. Secondary Fibres in Modern Pulp and Paper Technology. LesPromInform, 2015, no. 4(110), pp. 146–148. (In Russ.).
-
Area M.C., Popa V.I. Wood Fibres for Papermaking. Shawbury, Smithers Rapra Technology Ltd. Publ., 2014. 106 p.
-
Debnath M., Salem K.S., Naithani V., Musten E., Hubbe M.A., Pal L. Soft Mechanical Treatments of Recycled Fibers Using a High Shear Homogenizer for Tissue and Hygiene Product. Cellulose, 2021, vol. 28, pp. 7981–7994. https://doi.org/10.1007/s10570-021-04024-0
-
Ferdous T., Quaiyyum M.A., Bashar S., Jahan M.S. Anatomical, Morphological and Chemical Characteristics of Kaun Straw (Seetaria-ltalika). Nordic Pulp and Paper Research Journal, 2020, vol. 35, no. 2, pp. 288–298. https://doi.org/10.1515/npprj-2019-0057
-
Fischer W.J., Mayr M., Spirk S., Reishofer D., Jagiello L.A., Schmiedt R., Colson J., Zankel A., Bauer W. Pulp Fines – Characterization, Sheet Formation, and Comparison to Microfibrillated Cellulose. Polymers, 2017, vol. 9, iss. 8, art. no. 366. https://doi.org/10.3390/polym9080366
-
Gharehkhani S., Sadeghinezhad E., Kazi S.N., Yarmand H., Badarudin A., Safaei M.R., Zubir M.N. Basic Effects of Pulp Refining on Fiber Properties – A Review. Carbohydrate Polymers, 2015, vol. 115, pp. 785–803. https://doi.org/10.1016/j.carbpol.2014.08.047
-
Karlsson H., Rinnevuo T. Fibre Guide: Fibre Analysis and Process Applications in the Pulp and Paper Industry: A Handbook. Kista, AB Lorentzen & Wettre Publ., 2006. 120 p.
-
Hubbe M.A., Venditti R.A., Rojas O.J. What Happens to Cellulosic Fibers During Papermaking and Recycling? A Review. BioResources, 2007, vol. 2, no. 4, pp. 739–788. https://doi.org/10.15376/BIORES.2.4.739-788
-
ISO 16065-1:2014 Pulps – Determination of Fibre Length by Automated Optical Analysis. Part 1: Polarized Light Method. 2014. 10 p.
-
Johnsen I.A., Stenius P.I., Tammelin T., Österberg M., Johansson L., Laine J. The Influence of Dissolved Substances on Resin Adsorption to TMP Fine Material. Nordic Pulp and Paper Research Journal, 2006, vol. 21, no. 5, pp. 629–637. https://doi.org/10.3183/npprj-2006-21-05-p629-637
-
Luukko K., Kemppainen-Kajola P., Paulapuro H. Characterization of Mechanical Pulp Fines by Image Analysis. Appita Journal, 1997, vol. 50, pp. 387–392.
-
Mandlez D., Zangl-Jagiello L., Eckhart R., Bauer W. Softwood Kraft Pulp Fines: Application and Impact on Specific Refining Energy and Strength Properties. Cellulose, 2020, vol. 27, pp. 10359–10367. https://doi.org/10.1007/s10570-020-03467-1
-
Mayr M., Eckhart R., Thaller A., Bauer W. Characterization of Fines Quality and Their Independent Effect on Sheet Properties. In Advances in Pulp and Paper Research. Proceedings of the 16th Fund. Res. Symp. Oxford, 2017. Ed. by W. Batchelor, D. Söderberg. Manchester, FRC Publ., 2018, pp. 299–322. https://doi.org/10.15376/frc.2017.1.299
-
Motamedian H.R., Halilović A.E., Kulachenko A. Mechanisms of Strength and Stiffness Improvement of Paper After PFI Refining with a Focus on the Effect of Fines. Cellulose, 2019, vol. 26, pp. 4099–4124. https://doi.org/10.1007/s10570-019-02349-5
-
Popa V.I. Pulp Production and Processing: From Papermaking to High-Tech Products. Shawbury, Smithers Rapra Technology Ltd. Publ., 2013. 520 p
-
Pöhler T., Ketoja J.A., Lappalainen T., Luukkainen V., Nurminen I., Lahtinen P., Torvinen K. On the Strength Improvement of Lightweight Fibre Networks by Polymers, Fibrils and Fines. Cellulose, 2020, vol. 27, pp. 6961–6976. https://doi.org/10.1007/s10570-020-03263-x
-
Winter A., Gindl-Altmutter W., Mandlez D., Bauer W., Eckhart R., Leitner J., Veigel S. Reinforcement Effect of Pulp Fines and Microfibrillated Cellulose in Highly Densified Binderless Paperboards. Journal of Cleaner Production, 2021, vol. 115, art. no. 125258. https://doi.org/10.1016/j.jclepro.2020.125258
-
Wistara N.J., Young R.A. Properties and Treatments of Pulps from Recycled Paper. Part I. Physical and Chemical Properties of Pulps. Cellulose, 1999, vol. 6, pp. 291–324. https://doi.org/10.1023/A:1009221125962
Changes in the Morphological Characteristics of Secondary Fiber Obtained from Wet-Strength Paper During Gentle Refining of the Recycled Pulp. Part 2. Fines Characteristics. P. 169–179
|
Make a Submission
Lesnoy Zhurnal (Russian Forestry Journal) was awarded the "Seal of Recognition for Active Data Provider of the Year 2025"
|