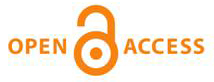
Address: 17 Naberezhnaya Severnoy Dviny, Arkhangelsk 163002 Russian Federation. Northern (Arctic) Federal University named after M.V.Lomonosov. Office 1425
Phone / Fax: (818-2) 21-61-18
E-mail: forest@narfu.ru
http://lesnoizhurnal.ru/en/

|
Structural Boards Made of Hydrodynamically Activated Pine (Pinus sylvestris) Bark without Binders. P. 175–187
|
 |

These works are licensed under a Creative Commons Attribution 4.0 International License.
Vladislav D. Eskin, Vladimir N. Ermolin, Anna I. Krivorotova
UDС
674.817
DOI:
10.37482/0536-1036-2024-5-175-187
Abstract
Bark is a large-tonnage waste in a number of wood processing technologies requiring efficient use. One of the promising areas of bark use is the production of boards without synthetic binders. Research has been conducted on the production of structural boards from Pinus sylvestris bark without a binder. The method is based on preliminary hydrodynamic activation of bark. The initial bark undergoes primary crushing in a hammer mill. After that, it is mixed with water at a concentration of 6 %. Then the resulting mass is activated in a rotary pulsation disperser, a carpet is formed from it, cold pressing is carried out, and then hot pressing. As a criterion for assessing the degree of mass activation, water-retaining capacity is adopted. The dependencies have been determined between the duration of treatment and water-retaining capacity, as well as the strength of the boards and water-retaining capacity. The latter made it possible to obtain the optimal value of the water-retaining capacity equal to 290 %. A multifactorial experiment has been conducted to develop the optimal hot pressing mode. As a result, the optimal mode for pressing the boards has been determined: temperature – 190 °C; specific process duration – 2.8 min/mm; pressing pressure – 4.4 MPa. The properties of the boards produced in this mode are: density – 980 kg/m 3 ; bending strength – 24 MPa; swelling during soaking for 24 hours – 5 %; water absorption – 9 %. After soaking and subsequent drying to a moisture content of 5 %, the boards retain 75 % of their before soaking. In this case, the geometric dimensions return to the original ones. The resulting boards can be used as a sheet finishing and structural material, in house-building (as a base for floor and roofing materials), in furniture production, especially in severe temperature and humidity conditions. The conducted research shows the possibility of producing board materials with high performance properties from pine bark without binders.
Keywordspine bark, boards, hydrodynamic activation, water-retaining capacity, fractional composition, strength, swelling, hot pressing
For citation
Eskin V.D., Ermolin V.N., Krivorotova A.I. Structural Boards Made of Hydrodynamically Activated Pine (Pinus sylvestris) Bark without Binders. Lesnoy Zhurnal = Russian Forestry Journal, 2024, no. 5, pp. 175–187. (In Russ.). https://doi.org/10.37482/0536-1036-2024-5-175-187
References
-
The appearance of the manufactured board samples Bayandin M.A., Ermolin V.N., Eliseev S.G. The Effect of Mechanical Activation on the Autohesive Properties of Wood. Khvoinye boreal’noi zony = Conifers of the Boreal Area, 2013, vol. XXXI, no. 1–2, pp. 159–163. (In Russ.).
-
Vakhnina T.N. Use of Wastes of Debarking for Production of Wood Chipboards. Problems of Reclamation of Household, Industrial and Agricultural Waste: IV International Scientific Ecological Conference (with the Participation of the Ecologists from Azerbaijan, Armenia, Belarus, Germany, Georgia, Kazakhstan, Kyrgyzstan, Latvia, Lebanon, Moldova, Transnistria, Russia, Slovakia, Uzbekistan and Ukraine). Krasnodar: KubSAU named after I.T. Trubilin, 2015, part 1, pp. 355–358. (In Russ.).
-
Devyatlovskaya A.N., Zhuravleva L.N., Devyatlovsky N.V. Utilization of Tree Bark from Wood Processing Enterprises. Aktual’nye problemy lesnogo kompleksa, 2010, no. 27, pp. 51–54. (In Russ.).
-
Dul’kin D.A. Development of Scientific Foundations and Improvement of the Processes of Paper and Cardboard Technology from Waste Paper: Doc. Tech. Sci. Diss. Abs. Arkhangelsk, 2008. 44 p. (In Russ.).
-
Evstigneev E.I. Chemistry of Wood. Saint-Petersburg, Polytechnic University Publ., 2007. 147 р. (In Russ.).
-
Eremin V.M. Comparative Anatomy of Pine Bark: Doc. Tech. Sci. Diss. Voronezh, 1983. 547 p. (In Russ.).
-
Ermolin V.N., Bayandin M.A., Kazitsin S.N., Namyatov A.V. Structure Formation of Low-Density Boards from Hydrodynamically Activated Soft Wood Waste. Lesnoy Zhurnal = Russian Forestry Journal, 2019, no. 5, pp. 148–157. (In Russ.). https://doi.org/10.17238/issn0536-1036.2019.5.148
-
Lazareva L.I., Chistova N.G., Medvedev S.O. The Use of Bark in Obtaining Wood-Fiber Plates. Khimija Rastitel’nogo Syr’ja, 2013, no. 1, pp. 235–238. (In Russ.). https://doi.org/10.14258/jcprm.1301235
-
Lotova L.I. Anatomy of the Bark of Conifers. Moscow, Nauka Publ., 1987. 160 p. (In Russ.).
-
Mus’ko N.P., Beusheva O.S., Saushkina S.S. Slab Materials Based on Modified Pine Bark. Polzunovskij vestnik, 2015, no. 2, pp. 136–138. (In Russ.).
-
Sudakova I.G., Garyntseva N.V., Kuznetsov B.N. Production of Wood-Based Panel Materials Using Binders Based on Birch Bark Suberin. Khimija Rastitel’nogo Syr’ja, 2011, no. 3, pp. 65–68. (In Russ.).
-
Fedosenko I.G. Evaluation of the Possibility of Using the Bark of Trees Growing in the Republic of Belarus for the Granulation. Trudy BGTU = Proceedings of BSTU, 2021, no. 2 (246), pp. 284–289. (In Russ.). https://doi.org/10.52065/2519-402X-2021-246-36-284-289
-
Tsyvin M.M. The Use of Tree Bark. Moscow, Lesnaya Promyshlennost’ Publ., 1973. 94 p. (In Russ.).
-
Cherkasova A.I., Zhuchenko A.G., Khlyupina D.P. Obtaining Slabs from Bark with a Binder. Tekhnologii drevesnykh plit i plastikov: Interuniversity Collection. Sverdlovsk, UPI Publ., 1980, iss. VII, pp. 76–82. (In Russ.).
-
Arzola-Alvarez A., Castillo-Castillo Y., Anderson R.С., Hume M., Ruiz-Barrera O., Min B.R., Arzola-Rubio A., Beier R.C., Salinas-Chavira J. Influence of Pine Bark Tannin on Bacterial Pathogens Growth and Nitrogen Compounds on Changes in Composted Poultry Litter. Brazilian Journal of Poultry Science, 2020, vol. 22, no. 1, pp. 1–10. http://dx.doi.org/10.1590/1806-9061-2018-0911
-
Berendt F., Pegel E., Blasko L., Cremer T. Bark Proportion of Scots Pine Industrial Wood. European Journal of Wood and Wood Products, 2021, vol. 79, pp. 749–752. https://doi.org/10.1007/s00107-021-01657-7
-
Fedorov V.S., Ryazanova T.V. Optimization of the Extraction Process of Pinus sylvestris L. Pine Bark with Monoethanolamine. VIII International Conference on Advanced Agritechnologies, Environmental Engineering and Sustainable Development (AGRITECH– VIII 2023), 2023, vol. 390, art. no. 05038. https://doi.org/10.1051/e3sconf/202339005038
-
Filbakk T., Jirjis R., Nurmi J., Høibø O. The Effect of Bark Content on Quality Parameters of Scots Pine (Pinus sylvestris L.) Pellets. Biomass and Bioenergy, 2011, vol. 35, iss. 8, pp. 3342–3349. https://doi.org/10.1016/j.biombioe.2010.09.011
-
Gößwald J., Barbu M.-C., Petutschnigg A., Tudor E.M. Binderless Thermal Insulation Panels Made of Spruce Back Fibres. Polymers, 2021, vol. 13, no. 11, art. no. 1799. https://doi.org/10.3390/polym13111799
-
Goring D.A.I. Thermal Softening, Adhesive Properties and Glass Transitions in Lignin, Hemicellulose and Cellulose. Consolidation of the Paper Web, 1965, pp. 555–568. https://doi.org/10.15376/frc.1965.1.555
-
Jayme G. Zellstoff und Papier, 1961, vol. 11, рp. 432–438. (In Germ.).
-
Kamperidou V., Lykidis C., Barmpoutis P. Utilization of Wood and Bark of Fast-Growing Hardwood Species in Energy Production. Journal of Forest Science, 2018, vol. 64 (4), pp. 164–170. https://doi.org/10.17221/141/2017-JFS
-
Lehtikangas P. Quality Properties of Pelletised Sawdust, Logging Residues and Bark. Biomass and Bioenergy, 2001, vol. 20, iss. 5, pp. 351–360. https://doi.org/10.1016/S0961-9534(00)00092-1
-
Margina Yu., Troegubov A., Kulikova Yu., Sliusar N. Composting Old Bark and Wood Waste in Cold Weather Conditions. Sustainability, 2023, vol. 15, no. 14, art. no. 10768. https://doi.org/10.3390/su151410768
-
Millers M., Magaznieks J. Scots Pine (Pinus sylvestris L.) Stem Wood and Bark Moisture and Density Influencing Factors. Research for Rural Development, 2012, pp. 91–97.
-
Nisca A., Stefănescu R., Stegărus D.I., Mare A.D., Farczadi L., Tanase C. Comparative Study Regarding the Chemical Composition and Biological Activity of Pine (Pinus nigra and P. sylvestris) Bark Extracts. Antioxidants, 2021, vol. 10, no. 2, art. no. 327. https://doi.org/10.3390/antiox10020327
-
Scalbert A. Antimicrobial Properties of Tannins. Phytochemistry, 1991, vol. 30, iss. 12, pp. 3875–3883. https://doi.org/10.1016/0031-9422(91)83426-L
-
Svoykin F., Birman A., Bacherikov I., Meter O., Bozhbov V. Perspectives of Bark Dump Recycling at Wood Processing Enterprises. IOP Conference Series: Materials Science and Engineering, 2020, vol. 817, art. no. 012033. https://doi.org/10.1088/1757-899X/817/1/012033
-
Terzopoulou P., Kamperidou V., Lykidis C. Cypress Wood and Bark Residues Chemical Characterization and Utilization as Fuel Pellets Feedstock. Forests, 2022, vol. 13, no. 8, art. no. 1303. https://doi.org/10.3390/f13081303
Structural Boards Made of Hydrodynamically Activated Pine (Pinus sylvestris) Bark without Binders. P. 175–187
|
Make a Submission
Lesnoy Zhurnal (Russian Forestry Journal) was awarded the "Seal of Recognition for Active Data Provider of the Year 2025"
|