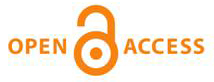
Address: 17 Naberezhnaya Severnoy Dviny, Arkhangelsk 163002 Russian Federation. Northern (Arctic) Federal University named after M.V.Lomonosov. Office 1425
Phone / Fax: (818-2) 21-61-18
E-mail: forest@narfu.ru
http://lesnoizhurnal.ru/en/

|
The Effect of the Knife Tacking Type on the Process of Producing Microcrystalline Cellulose. P. 152–165
|
 |

These works are licensed under a Creative Commons Attribution 4.0 International License.
Larisa V. Yurtayeva, Yuriy D. Alashkevich, Elena A. Slizikova, Evgeniy V. Kaplyov, Snezhana A. Pozharkova
UDС
676.154.3
DOI:
10.37482/0536-1036-2024-2-152-165
Abstract
The article shows the possibility of intensifying the process of producing microcrystalline cellulose via pregrinding of fibrous semi-finished products before hydrolysis. The technological factors determining the grinding of fibrous materials have been considered. The efficiency of the microcrystalline cellulose production process is influenced by the choice of its production technology. For grinding, a semi-industrial disc mill with a tacking with rectilinear and curvilinear knives has been used. Multiphysics models of the flow of fibrous mass in the grinding zone of a disc mill with different knife tacking patterns have been constructed. The morphological properties of the fiber have been measured on the Morfi Neo automatic fiber analyzer after grinding to 65 °SR. The nature of the change in the properties of bleached sulfate hardwood and softwood cellulose has been analyzed. It has been found that it is identical for all degrees of grinding, but the quantitative characteristics change to the greatest extent when grinding softwood cellulose using a tacking with rectilinear knives: the weighted average length of fibers decreases by 17 %, the width – by 14 %; the content of broken fibers increases by 22 %, the content of fines along the length – by 67 % and the fibrillation index – by 1.9 times. A comparative analysis of the values of the degree of polymerization depending on the knife tacking pattern has been carried out. The conditions for producing microcrystalline cellulose after grinding the fibrous mass in a semi-industrial disc mill, depending on the degree of grinding, have been determined. It has been shown that with an increase in the degree of grinding of the fibrous mass from 15 to 65 °SR, the degree of polymerization of microcrystalline cellulose decreases from 272 to 120, the concentration of hydrochloric acid – from 2.5 to 1.5 N and the duration of hydrolysis – from 120 to 90 min. The developed method for producing microcrystalline cellulose makes it possible to reduce the cost of chemical treatment of the fibrous mass (acid concentration, treatment duration and hydrolysis temperature) by 1.5 times.
Authors
Larisa V. Yurtayeva*, Candidate of Engineering, Assoc. Prof.; ResearcherID: ITU-6565-2023, ORCID: https://orcid.org/0009-0002-6045-3442
Yuriy D. Alashkevich, Doctor of Engineering, Prof.; ResearcherID: ITU-6674-2023, ORCID: https://orcid.org/0009-0005-9894-2630
Elena A. Slizikova, Postgraduate Student; ResearcherID: ITU-6598-2023, ORCID: https://orcid.org/0009-0003-2708-0653
Evgeniy V. Kaplyov, Postgraduate Student; ResearcherID: ITU-6526-2023, ORCID: https://orcid.org/0009-0005-0235-7630
Snezhana A. Pozharkova, Junior Research Scientist; ResearcherID: IUQ-1617-2023, ORCID: https://orcid.org/0009-0000-6403-1701
Keywordsgrinding of fibrous materials, microcrystalline cellulose, tacking, hydrolysis, fibrillation, disc mill, destruction, degree of polymerization
For citation
Yurtayeva L.V., Alashkevich Yu.D., Slizikova E.A., Kaplyov E.V., Pozharkova S.A. The Effect of the Knife Tacking Type on the Process of Producing Microcrystalline Cellulose. Lesnoy Zhurnal = Russian Forestry Journal, 2024, no. 2, pp. 152–165. (In Russ.). https://doi.
org/10.37482/0536-1036-2024-2-152-165
References
-
Alashkevich Yu.D. Fundamentals of the Theory of Hydrodynamic Processing of Fibrous Materials in Grinding Machines: Doc. Techn. Sci. Diss. Leningrad, 1980. 334 p. (In Russ.).
-
Alashkevich Yu.D., Reshetova N.S. Theory and Design of Machinery and Equipment in the Industry. Part 1. Krasnoyarsk, SibSTU Publ., 2013. 197 p. (In Russ.).
-
Alashkevich Yu.D., Reshetova N.S., Marchenko R.A. Theory and Design of Machinery and Equipment of the Branch: Practicum. Krasnoyarsk, Reshetnev Siberian State University of Science and Technology Publ., 2020. 96 p. (In Russ.).
-
Gause A.A., Goncharov V.N. Machines for Grinding and Sorting Paper Pulp: Lecture Notes. Leningrad, 1975. 115 p. (In Russ.).
-
Dyatlov E.S., Rublev A.I., Kondrashov A.I., Litvinov A.B. Disc Mills of Domestic Production for Pulp and Paper Industry. Tsellyulozno-bumazhnoe mashinostroenie, 1974, no. 1, pp. 1–5. (In Russ.).
-
Ivanov S.N. Paper Technology. 3rd ed. Moscow, Shkola Bumagi Publ., 2006. 696 p. (In Russ.).
-
Kaplyov E.V., Yurtayeva L.V., Alashkevich Yu.D., Tarazeev D.S. Investigation of Mechanical Strength Properties of Cellulose Obtained from Bio-Damaged Wood. Modern Trends in the Development of Chemical Technology, Industrial Ecology and Environmental Safety: Materials of the 3rd All-Russian Scientific and Practical Conference with the Participation of Young Scientists (St. Petersburg, April 7–8, 2022). St. Petersburg, Saint Petersburg State University of Industrial Technologies and Design Publ., 2022, pp. 25–28. (In Russ.).
-
Legotskiy S.S., Goncharov V.N. Grinding Equipment and Preparation of Paper Pulp. Moscow, Lesnaya promyshlennost’ Publ., 1990. 222 p. (In Russ.).
-
Legotskiy S.S., Laptev L.N. Paper Pulp Grinding. Moscow, Lesnaya promyshlennost’ Publ., 1981. 93 p. (In Russ.).
-
Obolenskaya A.V., Shchegolev V.P., Akim G.L., Akim E.L., Kossovich N.L., Emelyanova I.Z. Practical Work on the Chemistry of Wood and Pulp. Moscow, Lesnaya promyshlennost’ Publ., 1965. 411 p. (In Russ.).
-
Karmanov A.P., Kocheva L.S., Kiseleva A.A. Method for Producing Microcrystalline Cellulose. Patent RF, no. RU 2147057 С1, 2000. (In Russ.).
-
Tikhomirov A.V., Bulanov R.A. Method for Producing Microcrystalline Cellulose. Patent RF, no. RU 2155192 С1, 2000. (In Russ.).
-
Kuznetsov B.N., Danilov V.G., Yatsenkova O.V., Ibragimova E.F. Method for Producing Microcrystalline Cellulose from Cereal Straw. Patent RF, no. RU 2178033 С1, 2007. (In Russ.).
-
Alashkevich Yu.D., Kovalev V.I., Kharin V.F., Mukhachev A.P. Tacking. Patent RF, no. RU 2307833 С1, 2007. (In Russ.).
-
Alashkevich Yu.D., Kovalev V.I., Nabieva A.A. Tacking for a Disc Mill. Patent RF, no. RU 2314381 С1, 2008. (In Russ.).
-
Kuznetsov B.N., Danilov V.G., Yatsenkova O.V., Ibragimova E.F. Method for Producing Microcrystalline Cellulose from Autohydrolyzed Wood. Patent RF, no. RU 2395636 С1, 2010. (In Russ.).
-
Alashkevich Yu.D., Kovalev V.I., Yurtayeva L.V., Kaplyov E.V., Marchenko R.A. Method for Producing Microcrystalline Cellulose. Patent RF, no. 2797202 C1, 2023. (In Russ.).
-
Simigin P.S. On Grinding and Grinding Equipment. Bumazhnaya promyshlennost’, 1970, no. 6, pp. 15–17. (In Russ.).
-
Yurtayeva L.V., Alashkevich Yu.D. A Method for Producing Microcrystalline Cellulose Based on Bio-Damaged Wood. Khvoinye boreal’noi zony = Conifers of the Boreal Area, 2022, vol. XL, no. 2, pp. 158–163. (In Russ.). https://doi.org/10.53374/1993-0135-2022-2-158-163
-
Yurtayeva L.V., Alashkevich Yu.D., Kaplev E.V., Slizikova E.A. The Effect of Grinding Annual Plant Polymers on the Process of Obtaining Fine Cellulose. Khvoinye boreal’noi zony = Conifers of the Boreal Area, 2023, vol. XLI, no. 4, pp. 361–368. (In Russ.). https://doi.org/10.53374/1993-0135-2023-4-361-368
-
García Hernández M.A., Marure A.L., Neira Velázquez M.G., Mariano Torres J.A., Galvan A.A. Microcrystalline Cellulose Isolation – Proposed Mechanism: Enhanced Coupling. BioResources, 2023, vol. 18, iss. 1, pp. 1788–1802. https://doi.org/10.15376/biores.18.1.1788-1802
-
Hermawan D., Lai T.K., Jafarzadeh S.J., Gopakumar D.A., Hasan M., Owolabi F.A.T., Sri Aprilia N.A., Rizal S., Abdul Khalil H.P.S. Development of SeaweedBased Bamboo Microcrystalline Cellulose Films Intended for Sustainable Food Packaging Applications. BioResources, 2019, vol. 14, iss. 2, pp. 3389–3410. https://doi.org/10.15376/biores.14.2.3389-3410
-
Hou W., Ling C., Shi S., Yan Z. Preparation and Characterization of Microcrystalline Cellulose from Waste Cotton Fabrics by Using Phosphotungstic Acid. International Journal of Biological Macromolecules, 2019, vol. 123, pp. 363–368. https://doi.org/10.1016/j.ijbiomac.2018.11.112
-
Ilyas R.A., Sapuan S.M., Ishak M.R., Zainudin E.S., Atikah M.S. Characterization of Sugar Palm Nanocellulose and its Potential for Reinforcement with a Starch-Based Composite. Sugar Palm Biofibers, Biopolymers, and Biocomposites. 1st ed. Boca Raton, CRC Press, 2018, chapt. 10. https://doi.org/10.1201/9780429443923-10
-
Kale R.D., Bansal P.S., Gorade V.G. Extraction of Microcrystalline Cellulose from Cotton Sliver and its Comparison with Commercial Microcrystalline Cellulose. Journal of Polymers and the Environment, 2018, vol. 26, pp. 355–364. https://doi.org/10.1007/S10924-017-0936-2
-
Kushnir E.Yu., Autlov S.A., Bazarnova N.G. Preparation of Microcrystalline Cellulose Directly from Wood under Microwave Radiation. Russian Journal of Bioorganic Chemistry, 2015, vol. 41, pp. 713–718. https://doi.org/10.1134/S1068162015070079
-
Li T., Chen C., Brozena A.H., Hu L., Zhu J.Y., Xu L., Driemeier C., Dai J., Rojas O.J., Isogai A., Wågberg L., Hu L. Developing Fibrillated Cellulose as a Sustainable Technological Material. Nature, 2021, vol. 590, pp. 47–56. https://doi.org/10.1038/s41586-020-03167-7
-
Microcrystalline Cellulose (MCC) Market by Source Type and Application: Global Opportunity Analysis and Industry Forecast 2018 – 2025. Portland, Allied Market Research, 2018. 212 p.
-
Queiroz A.L.P., Kerins B.M., Yadav J., Farag F., Faisal W., Crowley M.E., Lawrence S.E., Moynihan H.A., Healy A.-M., Vucen S., Crean A.M. Investigating Microcrystalline Cellulose Crystallinity using Raman Spectroscopy. Cellulose, 2021, vol. 28, pp. 8971–8985. https://doi.org/10.1007/s10570-021-04093-1
-
Tan W.Y., Gopinath S.C.B., Anbu P., Velusamy P., Gunny A.A.N., Chen Y., Subramaniam S. Generation of Microcrystalline Cellulose from Cotton Waste and its Properties. BioResources, 2023, vol. 18, iss. 3, pp. 4884–4896. https://doi.org/10.15376/ biores.18.3.4884-4896
-
Vasilyeva D.Yu., Yurtaeva L.V., Marchenko R.A., Kaplyov E.V., Zyryanov D.E., Reshetova N.S. Investigation of the Influence of the Pattern of a Disc Mill Set on the Process of Obtaining Powdered Pulp. Journal of Physics: Conference Series, 2021, Krasnoyarsk, vol. 2094, art. no. 042050. https://doi.org/10.1088/1742-6596/2094/4/042050
The Effect of the Knife Tacking Type on the Process of Producing Microcrystalline Cellulose. P. 152–165
|
Make a Submission
Lesnoy Zhurnal (Russian Forestry Journal) was awarded the "Seal of Recognition for Active Data Provider of the Year 2025"
|