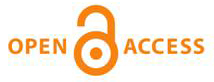
Address: 17 Naberezhnaya Severnoy Dviny, Arkhangelsk 163002 Russian Federation. Northern (Arctic) Federal University named after M.V.Lomonosov. Office 1425
Phone / Fax: (818-2) 21-61-18
E-mail: forest@narfu.ru
http://lesnoizhurnal.ru/en/

|
Modeling of the Rotary Mechanism of the Hydraulic Manipulator of a Timber Truck. P. 143–158
|
 |

These works are licensed under a Creative Commons Attribution 4.0 International License.
Valeryi I. Posmetyev, Vadim O. Nikonov, Andrey Yu. Manukovskii, Viktor V. Posmetyev, Igor V. Kazakov
UDС
621.225:69.002.51
DOI:
10.37482/0536-1036-2024-5-143-158
Abstract
The importance of loading and unloading operations in the technological process of wood hauling by timber trucks, as well as the need to improve the design of hydraulic manipulators, are considered. The most rational ways to increase the efficiency of their functioning are given. The disadvantages of traditional designs of hydraulic manipulator rotary mechanisms based on rack-and-pinion gears are presented. An improved design of the crank rotary mechanism of the hydraulic manipulator column from six hydraulic cylinders is proposed. The research methodology is based on the use of mathematical modeling. It has been revealed that the accumulated energy for one braking cycle when moving the load is about 1442 J. Considering that timber loading is carried out at a height of approximately 2 m, the recovery system allows approximately 12 % of the rotation energy to be directed to the load lifting operation. Over the entire range of change in the angle of the end of rotation, the recovered energy varies by only 7.1 % – from 1340 to 1442 J, and the load swing amplitude – by 1.2 % – from 0.336 to 0.340 m. It has been determined that with an increase in the length of the guide, the recovered energy decreases slightly – from 1564 to 1428 J (by 8.7 %) – and the load swing amplitude – from 0.344 to 0.339 (by 1.5 %). It has been found that over the entire angular range, the recovered energy varies from 1399 to 1442 J (by 3 %), and the load swing amplitude – from 0.3380 to 0.3393 m (by 0.4 %). The angular unevenness of the recovery efficiency indicators is no more than 3 %. To study the influence of the parameters of the crank rotary mechanism of the hydraulic manipulator column on the efficiency of energy recovery, a multifactor optimization problem has been solved. It has been established that the optimal value of the distance from the crank axis to the movable axes of the hydraulic cylinders of the rotary mechanism of the hydraulic manipulator column is 0.23–0.25 m, the optimal value of the displacement of the crank axis relative to the axis of the manipulator column is 0.17–0.18 m. At the same time, the recovered energy for 1 cycle of load moving is at least 1500 J, and the amplitude of the load swing is no more than 0.35 m.
Authors
Valeryi I. Posmetyev1, Doctor of Engineering, Prof.; ResearcherID: Q-1411-2015, ОRCID: https://orcid.org/0000-0001-9878-7451
Vadim O. Nikonov1*, Candidate of Engineering, Assoc. Prof.; ResearcherID: N-3510-2019, ORCID: https://orcid.org/0000-0002-7380-9180
Andrey Yu. Manukovskii1, Doctor of Engineering, Prof.; ResearcherID: AAR-1976-2020, ORCID: https://orcid.org/0000-0003-4289-6581
Viktor V. Posmetyev1, Candidate of Physics and Mathematics, Assoc. Prof.; ResearcherID: Z-3736-2019, ОRCID: https://orcid.org/0000-0001-6622-5358
Igor V. Kazakov2, Doctor of Engineering, Leading Research Scientist; ResearcherID: AAD-8084-2020, ОRCID: https://orcid.org/0009-0001-2719-375X
Affiliation
1Voronezh State University of Forestry and Technologies named after G.F. Morozov, ul. Timiryazeva, 8, Voronezh, 394087, Russian Federation; posmetyev@mail.ru, 8888nike8888@mail.ru*, mayu1964@mail.ru, victorvpo@mail.ru
2All-Russian Research Institute of Forestry and Forestry Mechanization, ul. Institutskaya, 15, Pushkino, Moscow Region, 141202, Russian Federation; igor.kazakov2015@bk.ru
Keywordscolumn crank rotary mechanism, timber truck, hydraulic manipulator, hydraulic cylinders, energy recovery, timber, handling operations, performance indicators, hydropneumatic accumulator
For citation
Posmetyev V.I., Nikonov V.O., Manukovskii A.Yu., Posmetyev V.V., Kazakov
I.V. Modeling of the Rotary Mechanism of the Hydraulic Manipulator of a Timber Truck. Lesnoy Zhurnal = Russian Forestry Journal, 2024, no. 5, pp. 143–158. (In Russ.). https://doi.org/10.37482/0536-1036-2024-5-143-158
References
-
Adler Yu.P., Markova E.V., Granovskij Yu.V. Planning an Experiment When Searching for Optimal Conditions. 2nd ed., revised and enlarged. Moscow, Nauka Publ., 1976. 279 p. (In Russ.).
-
Granovskij V.A., Siraya T.N. Methods for Processing Experimental Data during Measurements. Leningrad, Energoatomizdat Publ., 1990. 288 p. (In Russ.).
-
Mudrov A.E. Numerical Methods for PC in Basic, Fortran and Pascal Languages. Tomsk, Rasko Publ., 1991. 270 p. (In Russ.).
-
Nikonov V.O. Current State, Problems and Ways to Improve the Efficiency of Timber Road Transport. Voronezh, Voronezh State University of Forestry and Techonlogies named after G.F. Morozov Publ., 2021. 203 p. (In Russ.).
-
Posmetiev V.I., Nikonov V.O. On the Impact of Traditional Designs of Hydromanipulators on the Efficiency of Forest Road Transport. Problems of Operation of Automobile Transport and Ways of Their Solution Based on Advanced Technologies and Scientific and Technical Solutions: Materials of the All-Russian Scientific and Technical Conference. Voronezh, Voronezh State University of Forestry and Techonlogies named after G.F. Morozov Publ., 2022, pp. 24–31. (In Russ.). https://doi.org/10.58168/PRTOW2022_24-31
-
Cheng M., Luo S., Ding R., Xu B., Zhang J. Dynamic Impact of Hydraulic Systems Using Pressure Feedback for Active Damping. Applied Mathematical Modelling, 2021, vol. 89, part 1, pp. 454–469. https://doi.org/10.1016/j.apm.2020.07.043
-
Han J., Wang F., Sun C. Trajectory Tracking Control of a Manipulator Based on an Adaptive Neuro-Fuzzy Inference System. Applied Sciences, 2023, vol. 13, no. 2, art. no. 1046. https://doi.org/10.3390/app13021046
-
Kim M., Lee S.-U., Kim S.-S. Real-Time Simulator of a Six Degree-of-Freedom Hydraulic Manipulator for Pipe-Cutting Applications. IEEE Access, 2021, vol. 9, pp. 153371– 153381. https://doi.org/10.1109/ACCESS.2021.3127502
-
Li L., Lin Z., Jiang Y., Yu C., Yao J. Valve Deadzone / Backlash Compensation for Lifting Motion Control of Hydraulic Manipulators. Machines, 2021, vol. 9, no. 3, art. no. 57. https://doi.org/10.3390/machines9030057
-
Li P., Li Y. Research on the Electro-Hydraulic Servo System of Picking Manipulator. AIP Advances, 2023, vol. 13, iss. 1, art. no. 015312. https://doi.org/10.1063/5.0130344
-
Łopatka M.J., Krogul P., Rubiec A., Przybysz M. Preliminary Experimental Research on the Influence of Counterbalance Valves on the Operation of a Heavy Hydraulic Manipulator during Long-Range Straight-Line Movement. Energies, 2022, vol. 15, no. 15, art. no. 5596. https://doi.org/10.3390/en15155596
-
Posmetev V.I., Nikonov V.O., Posmetev V.V. Imitating Modeling Results of a Recuperative Hydraulic Subsystem of the Timber Truck Manipulator. IOP Conference Series: Earth and Environmental Science, 2019, vol. 392, art. no. 012038. https://doi.org/10.1088/1755-1315/392/1/012038
-
Renner A., Wind H., Sawodny O. Online Payload Estimation for Hydraulically Actuated Manipulators. Mechatronics, 2020, vol. 66, art. no. 102322. https://doi.org/10.1016/j.mechatronics.2020.102322
-
Truong H.V.A., Trinh H.A., Ahn K.K. Truong Safety Operation of n-DOF Serial Hydraulic Manipulator in Constrained Motion with Consideration of Contact-Loss Fault. Applied Sciences, 2020, vol. 10, no. 22, art. no. 8107. https://doi.org/10.3390/app10228107
-
Wei X., Ye J., Xu J., Tang Z. Adaptive Dynamic Programming-Based Cross-Scale Control of a Hydraulic-Driven Flexible Robotic Manipulator. Applied Sciences, 2023, vol. 13, no. 5, art. no. 2890. https://doi.org/10.3390/app13052890
-
Xia Y., Nie Y., Chen Z., Lyu L., Hu P. Motion Control of a Hydraulic Manipulator with Adaptive Nonlinear Model Compensation and Comparative Experiments. Machines, 2022, vol. 10, no. 3, art. no. 214. https://doi.org/10.3390/machines10030214
-
Yang X., Deng W., Yao J. Neural Adaptive Dynamic Surface Asymptotic Tracking Control of Hydraulic Manipulators with Guaranteed Transient Performance. IEEE Transactions on Neural Networks and Learning Systems, 2023, vol. 34, no. 10, pp. 7339– 7349. https://doi.org/10.1109/TNNLS.2022.3141463
-
Zhang X., Shi G. Dual Extended State Observer-Based Adaptive Dynamic Surface Control for a Hydraulic Manipulator with Actuator Dynamics. Mechanism and Machine Theory, 2022, vol. 169, art. no. 104647. https://doi.org/10.1016/j.mechmachtheory.2021.104647
-
Zheng S., Ding R., Zhang J., Xu B. Global Energy Efficiency Improvement of Redundant Hydraulic Manipulator with Dynamic Programming. Energy Conversion and Management, 2021, vol. 230, art. no. 113762. https://doi.org/10.1016/j.enconman.2020.113762
-
Zhou S., Shen C., Zhu S., Li W., Nie Y., Chen Z. A Teleoperation Framework Based on Heterogeneous Matching for Hydraulic Manipulator. Machines, 2022, vol. 10, no. 7, art. no. 536. https://doi.org/10.3390/machines10070536
Modeling of the Rotary Mechanism of the Hydraulic Manipulator of a Timber Truck. P. 143–158
|
Make a Submission
Lesnoy Zhurnal (Russian Forestry Journal) was awarded the "Seal of Recognition for Active Data Provider of the Year 2025"
|