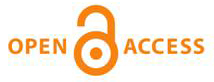
Address: Naberezhnaya Severnoy Dviny, 17, Arkhangelsk, 163002, Russian Federation, Northern (Arctic) Federal University named after M.V.Lomonosov, office 1425
Phone: +7 (8182) 21-61-18
E-mail: forest@narfu.ru
http://lesnoizhurnal.ru/en/
|
Effect of Topological Structure of Cellulose on the Processes of Acetylation and Nitration. C. 176-189
|
 |
K.S. Vashukova, K.Y. Terentyev, D.G. Chukhchin, A.D. Ivakhnov, D.N. Poshina
UDС
663.18:661.728
DOI:
10.37482/0536-1036-2023-6-176-189
Abstract
Cellulose esters are actively used in the production of new by-products, drugs, and materials. Plant raw materials are the main source for the production of cellulose derivatives. The production of cellulose by microbial synthesis is also becoming promising. Despite similar pathways of microfibril biosynthesis, cellulose samples of plant and bacterial origin differ in a number of structural features. The aim of this work is to evaluate the influence of the topological structure of cellulose of plant and bacterial origin on the acetylation and nitration processes. Cotton and kraft cellulose were used as samples of plant cellulose. Bacterial cellulose was obtained in the laboratory using a mixed community of microorganisms under static conditions on synthetic glucose media. Nitration of cellulose samples was carried out with a mixture of concentrated sulfuric and nitric acids; and the degree of substitution was calculated from the nitrogen content determined by the ferrosulfate method. The IR spectra of samples of the original cotton cellulose, as well as nitrates of bacterial and cotton cellulose, were recorded on a Vertex-70 infrared Fourier spectrometer in the range of wave numbers 4000…400 cm–1. Cellulose acetylation was carried out in supercritical carbon dioxide by direct acetylation in an SFE-5000 supercritical fluid extraction system, Thar Process. The content of bound acetic acid in cellulose acetate was determined titrimetrically and then the degree of substitution was calculated. Fibers of plant cellulose and fibrils of bacterial cellulose were visualized by electron and atomic force microscopy. The yield of nitrate from pure cotton cellulose was 160 %, i.e., the degree of substitution was 2.20. Cellulose nitrate obtained from bacterial cellulose under similar conditions had a degree of substitution of 1.96. A new method of direct acetylation of lyophilically dried preparations of bacterial cellulose in supercritical carbon dioxide was proposed, which allows the process to be carried out without acid catalyst and at reduced consumption of acetylating agent. Acetylation of plant kraft cellulose showed a degree of substitution of 2.40, for bacterial cellulose – yield of diacetyl cellulose with the content of acetyl groups 50 %, this corresponds to the degree of substitution of 2.10. The obtaining of esters is due to both topochemical features of microfibrils and crystallinity of the material.
Authors
Кsenia S. Vashukova1*, Candidate of Engineering, Assoc. Prof.; ResearcherID: G-1760-2019, ORCID: https://orcid.org/0000-0002-7916-2410
Konstantin Y. Terentyev1, Candidate of Engineering, Assoc. Prof.; ResearcherID: N-1755-2016, ORCID: https://orcid.org/0000-0002-4042-7864
Dmitry G. Chukhchin1, Candidate of Engineering, Prof.; ResearcherID: O-9487-2015, ORCID: https://orcid.org/0000-0003-3250-8469
Artem D. Ivakhnov1, Candidate of Chemistry, Senior Research Scientist; ResearcherID: U-4822-2019, ORCID: https://orcid.org/0000-0003-2822-9192
Daria N. Poshina2, Candidate of Engineering, Research Scientist; ResearcherID: E-8413-2017, ORCID: https://orcid.org/0000-0001-5342-0605
Affiliation
1Northern (Arctic) Federal University named after M.V. Lomonosov, Naberezhnaya Severnoy Dviny, 17, Arkhangelsk, 163002, Russian Federation; k.bolotova@narfu.ru*, k.terentev@narfu.ru, dimatsch@mail.ru, a.ivahnov@narfu.ru
2 Institute of Macromolecular Compounds of the Russian Academy of Sciences, Bolshoy pr., 31, Saint-Petersburg, 199004, Russian Federation; poschin@yandex.ru
Keywordscellulose fibers, cellulose acetate, cellulose nitrate, bacterial cellulose, plant cellulose, cellulose esters
For citation
Vashukova K.S., Terentyev K.Y., Chukhchin D.G., Ivakhnov A.D., Poshina D.N. Effect of Topological Structure of Cellulose on the Processes of Acetylation and Nitration. Lesnoy Zhurnal = Russian Forestry Journal, 2023, no. 6, pp. 176–189. (In Russ.). https://doi.org/10.37482/0536-1036-2023-6-176-189
References
- Bellami L. Infrared Spectra of Complex Molecules. Moscow, Foreign literature Publ., 1963. 590 p. (In Russ.).
- Bolotova K.S., Buyuklinskaya O.V., Chistyakova A.S., Travina O.V., Chukhchin D.G. Production and in vivo Toxicity Testing of Microcrystalline Cellulose Derived from Bacterial Cellulose. Ekologiya cheloveka = Human ecology, 2018, no. 2, pp. 21–25. (In Russ.). https://doi.org/10.33396/1728-0869-2018-2-21-25
- Bolotova K.S., Chukhchin D.G., Majer L.V., Guryanova A.A. Morphological Features of the Fibrillar Structure of Plant and Bacterial Cellulose. Lesnoy Zhurnal = Russian Forestry Journal, 2016, no. 6, pp. 153–165. (In Russ.). https://doi.org/10.17238/issn0536-1036.2016.6.153
- Bolotova K.S., Vydrina I.V., Chukhchin D.G., Novozhilov E.V., Sinelnikov I.G., Rudakova V.A., Terentyev K.Y., Kanarskiy A.V. Composition of the Medusomyces gisevii Community and the Properties of Bacterial Cellulose Synthesized by Them. Vestnik tekhnologicheskogo universiteta = Bulletin of the Technological University, 2019, vol. 22, no. 10, pp. 39–43. (In Russ.).
- Vinogradova V.R., Bolotova K.S. Influence of Chemical and Enzymatic Treatment on the Component Composition and Structure of Material Based on Bacterial Cellulose. Biotechnologies in the Chemical-Forestry Complex: Proceedings of the Scientific Conf. Arkhangelsk, 2014, pp. 118–122. (In Russ.).
- Gensh K.V., Kolosov P.V., Bazarnova N.G. Quantitative Analysis of Cellulose Nitrates by FT-IR Spectroscopy. Khimija Rastitel’nogo Syr’ja = Chemistry of plant raw material, 2010, no. 1, pp. 63–66. (In Russ.).
- Ivahnov A.D., Bogolicyn K.G., Skrebec T.E. Preparation of Secondary Cellulose Acetate by Direct Acetylation in Supercritical Carbon Dioxide. Lesnoy Zhurnal = Russian Forestry Journal, 2010, no. 3, pp. 114–119. (In Russ.).
- Kovalenko V.I. Molecular Structural Heterogeneity of Cellulose Nitrates. Uspekhi himii = Russian Chemical Reviews, 1995, vol. 64, no. 8, pp. 803–817. (In Russ.).
- Panchenko O.A., Titova O.I. Problems and Achievements in the Production of Cellulose Nitrates. Khimija Rastitel’nogo Syr’ja = Chemistry of plant raw material, 2005, no. 3, pp. 85–88. (In Russ.).
- Bahmid N.A., Syamsu K., Maddu A. Production of Cellulose Acetate from Oil Palm Empty Fruit Bunches Cellulose. Chemical and Process Engineering Research, 2013, vol. 17, iss. 21, pp. 12–20.
- Bolotova K., Travina O., Chukhchin D., Novozhilov E. The Morphological Structure of Microcrystallites Derived from Plant and Bacterial Cellulose. Nano, Bio and Green-Technologies for a Sustainable Future: 17th International Multidisciplinary Scientific Geoconference SGEM 2017. Sofia, STEF92 Technology Ltd., 2017, vol. 17, pp. 407–412. https://doi.org/10.5593/sgem2017/61/S24.053
- Budaeva V.V., Gismatulina Y.A., Mironova G.F., Skiba E.A., Gladysheva E.K., Kashcheyeva E.I., Baibakova O.V., Korchagina A.A., Shavyrkina N.A., Golubev D.S., Bychin N.V., Pavlov I.N., Sakovich G.V. Bacterial Nanocellulose Nitrates. Nanomaterials, 2019, vol. 9, iss. 12, art. 1694. https://doi.org/10.3390/nano9121694
- Chang C., Zhang L. Cellulose-based Hydrogels: Present Status and Application Prospects. Carbohydrate Polymers, 2011, vol. 84, iss. 1, pp. 40–53. https://doi.org/10.1016/j.carbpol.2010.12.023
- Cheng H.N., Dowd M.K., Selling G.W., Biswas A. Synthesis of Cellulose Acetate from Cotton Byproducts. Carbohydrate polymers, 2010, vol. 80, iss. 2, pp. 449–452. https://doi.org/10.1016/j.carbpol.2009.11.048
- Feng T., Deng C., Xue Q., Wang Y., Huang J., Xiang Q. Bamboo Pulp Fiber Suitable for Nitrocellulose, Cellulose Acetate and Cellulose Fiber and its Production Method. Patent China, no. CN1995495B, 2006.
- Geyer U., Heinze T., Stein A., Klemm D., Marsch S., Schumann D., Schmauder H.P. Formation, Derivatization and Applications of Bacterial Cellulose. International Journal of Biological Macromolecules, 1994, vol. 16, iss. 6, pp. 343–347. https://doi.org/10.1016/0141-8130(94)90067-1
- Huang Y., Zhu C., Yang J., Nie Y., Chen C., Sun D. Recent Advances in Bacterial Cellulose. Cellulose, 2014, vol. 21, iss. 1, pp. 1–30. https://doi.org/10.1007/s10570-013-0088-z
- Ifuku S., Nogi M., Abe K., Handa K., Nakatsubo F., Yano H. Surface Modification of Bacterial Cellulose Nanofibers for Property Enhancement of Optically Transparent Composites: Dependence on Acetyl-Group DS. Biomacromolecules, 2007, vol. 8, iss. 6, pp. 1973–1978. https://doi.org/10.1021/bm070113b
- Israel A.U., Obot I.B., Umoren S.A., Mkpenie V., Asuquo J.E. Production of Cellulosic Polymers from Agricultural Wastes. E-Journal of Chemistry, 2008, vol. 5, iss. 1, pp. 81–85. https://doi.org/10.1155/2008/436356
- Jamal S.H., Roslan N.J., Shah N.A.A., Noor S.A.M., Ong K.K., Yunus W.M.Z.W. Preparation and Characterization of Nitrocellulose from Bacterial Cellulose for Propellant Uses. Materials Today: Proceedings, 2020, vol. 29, pp. 185–189. https://doi.org/10.1016/j.matpr.2020.05.540
- Liu J. Nitrate Esters Chemistry and Technology. Singapore, Springer, 2019. 684 p. https://doi.org/10.1007/978-981-13-6647-5
- Liu J.P. Method of Making Nitrocellulose from Eulaliopsis Binata as Raw Material. Patent China, no. CN1011970, 1991.
- Luo Q., Zhu J., Li Z., Duan X., Pei C., Mao C. The Solution Characteristics of Nitrated Bacterial Cellulose in Acetone. New Journal of Chemistry, 2018, vol. 42, iss. 22, pp. 18252–18258. https://doi.org/10.1039/C8NJ02018C
- Malkov A., Tyshkunova I., Vidrina I., Novozhilov E. Diffractometric Method for Determining the Crystallinity Degree of Cellulose. 18th International Multidisciplinary Scientific Geoconference, SGEM 2018. Vienna, Austria, 2018, vol. 18, iss. 6.4, pp. 119–126. https://doi.org/10.5593/sgem2018V/6.4/S08.016
- Mattar H., Baz Z., Saleh A., Shalaby A.S., Azzazy A.E., Salah H., Ismail I. Nitrocellulose: Structure, Synthesis, Characterization, and Applications. Water, Energy, Food and Environment Journal, 2020, no. 3, pp. 1–15.
- Qiu K., Netravali A.N. A Review of Fabrication and Applications of Bacterial Cellulose Based Nanocomposites. Polymer Reviews, 2014, vol. 54, iss. 4, pp. 598–626. https://doi.org/10.1080/15583724.2014.896018
- Reiniati I., Hrymak A.N., Margaritis A. Recent Developments in the Production and Applications of Bacterial Cellulose Fibers and Nanocrystals. Critical Reviews in Biotechnology, 2017, vol. 37, iss. 4, pp. 510–524. https://doi.org/10.1080/07388551.2016.1189871
- Rodrigues Filho G., Monteiro D.S., da Silva Meireles C., de Assunção R.M.N., Cerqueira D.A., Barud H.S., Ribeiro S.J.L., Messadeq Y. Synthesis and Characterization of Cellulose Acetate Produced from Recycled Newspaper. Carbohydrate Polymers, 2008, vol. 73, iss. 1, pp. 74–82. https://doi.org/10.1016/j.carbpol.2007.11.010
- Rodrigues Filho G., da Cruz S.F., Pasquini D., Cerqueira D.A., de Souza Prado V., de Assunção R.M.N. Water Flux Through Cellulose Triacetate Films Produced from Heterogeneous Acetylation of Sugar Cane Bagasse. Journal of Membrane Science, 2000, vol. 177, iss. 1–2, pp. 225–231. https://doi.org/10.1016/S0376-7388(00)00469-5
- Sato H., Uraki Y., Kishimoto T., Sano Y. New Process for Producing Cellulose Acetate from Wood in Concentrated Acetic Acid. Cellulose, 2003, vol. 10, pp. 397–404. https://doi.org/10.1023/A:1027359708581
- Samadian H., Maleki H., Allahyari Z., Jaymand M. Natural Polymers-based LightInduced Hydrogels: Promising Biomaterials for Biomedical Applications. Coordination Chemistry Reviews, 2020, vol. 420, art. 213432. https://doi.org/10.1016/j.ccr.2020.213432
- Shevchenko A.R., Tyshkunova I.V., Chukhchin D.G., Malkov A.V., Toptunov E.A., Telitsin V.D., Rozhkova A.M., Sinitsyna O.A., Gofman I.V., Aksenov A.S. Production of Biomodified Bleached Kraft Pulp by Catalytic Conversion Using Penicillium verruculosum Enzymes: Composition, Properties, Structure and Application. Catalysts, 2023, vol. 13, iss. 1, art. 103. https://doi.org/10.3390/catal13010103.
- Schlufter K., Schmauder H.P., Dorn S., Heinze T. Efficient Homogeneous Chemical Modification of Bacterial Cellulose in the Ionic Liquid 1‐N‐butyl‐3‐Methylimidazolium Chloride. Macromolecular Rapid Communications, 2006, vol. 27, iss. 19, pp. 1670–1676. https://doi.org/10.1002/marc.200600463
- Speicher N.L., Li P.Z., Wallace I.S. Phosphoregulation of the Plant Cellulose Synthase Complex and Cellulose Synthase-Like Proteins. Plants, 2018, vol. 7, iss. 3. 52 p. https://doi.org/10.3390/plants7030052
- Sun D.P., Ma B., Zhu C.L., Liu C.S., Yang J.Z. Novel Nitrocellulose Made from Bacterial Cellulose. Journal of Energetic Materials, 2010, vol. 28, iss. 2, pp. 85–97. https://doi.org/10.1080/07370650903222551
- Sunasee R., Hemraz U.D., Ckless K. Cellulose Nanocrystals: a Versatile Nanoplatform for Emerging Biomedical Applications. Expert Opinion on Drug Delivery, 2016, vol. 13, iss. 9, pp. 1243–1256. https://doi.org/10.1080/17425247.2016.1182491
- Vydrina I., Malkov A., Vashukova K., Tyshkunova I., Mayer L., Faleva A., Shestakov S., Novozhilov E., Chukhchin D. A New Method for Determination of Lignocellulose Crystallinity from XRD Data using NMR Calibration. Carbohydrate Polymer Technologies and Applications, 2023, vol. 5, art. 100305. https://doi.org/10.1016/j.carpta.2023.100305
- Yamamoto H., Horii F., Hirai A. Structural Studies of Bacterial Cellulose through the Solid-Phase Nitration and Acetylation by CP/MAS 13 C NMR Spectroscopy. Cellulose, 2006, vol. 13, pp. 327–342. https://doi.org/10.1007/s10570-005-9034-z
- Yıldız Ş., Morcali M.H., Ziba C.A., Copcu B., Dolaz M. Synthesis and Characterization of Cellulose Derivatives from Industrial Towel Waste. ChemistrySelect, 2019, vol. 4, iss. 28, pp. 8358–8364. https://doi.org/10.1002/slct.201900398
|
Make a Submission
Lesnoy Zhurnal (Russian Forestry Journal) was awarded the "Seal of Recognition for Active Data Provider of the Year 2024"
|