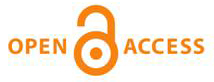
Address: Naberezhnaya Severnoy Dviny, 17, Arkhangelsk, 163002, Russian Federation, Northern (Arctic) Federal University named after M.V.Lomonosov, office 1425
Phone: +7 (8182) 21-61-18
E-mail: forest@narfu.ru
http://lesnoizhurnal.ru/en/
|
Deriving Biocomposites of Polymer Phase Plasticised Cellulose Acetates with Varying Degrees of Acetylation. P. 155–168
|
 |
Shkuro A.E., Glukhikh V.V., Usova K.A., Chirkov D.D., Zakharov P.S., Vurasko A.V.
UDС
006.82
DOI:
10.37482/0536-1036-2023-4-155-168
Abstract
It is anticipated that the creation of wood-polymer composites (WPC) made of naturally renewable polymers and their derivatives (biocomposites) would have a significant practical use due to the rise in prices for synthetic thermoplastic polymers derived from oil and gas. Furthermore, the necessity to replace synthetic polymers such as polyethylene, polypropylene, polyvinyl chloride, and others as components of composite materials is also associated with environmental hazards caused by their low degradation rate in the natural media (soil, water, and air). A further problem for manufacturers of WPC is the legislative requirement for autonomous neutralisation of production waste. One of the potential materials for practical application in the production of WPC are binders based on plasticised cellulose acetates. Russian and foreign scientists have studied the influence of the degree of acetylation of cellulose acetate on the properties of polymeric materials that do not contain lignocellulose fillers. There is no information found concerning the secondary use of cellulose acetate waste for the production of WPC. This article presents the results of an investigation into the hot pressing of biocomposites with a polymer phase of plasticised cellulose acetates of varying degrees of acetylation and fillers: wood flour and waste acetate photographic film. An experimental and statistical dependence of the effect of the degree of acetylation of cellulose acetate and filler content in the biocomposite on its properties was developed, sufficient to exceed a confidence level of 0.9. The experimental specifications included decomposition in activated soil, water absorption, bending strength, Brinell hardness, etc. Some test results showed that the derived biocomposites have the same level of properties as the reference WPC, which consists of a high-density polyethylene phase with a wood flour content of 50 %. The derived dependencies allow us to predict changes in the properties of biocomposites at different degrees of acetylation of plasticised cellulose acetate and filler content. Moreover, they solve the problem of choosing the optimal chemical combination for WPC for manufacturing a specific product by hot pressing.
Authors
Aleksey E. Shkuro*, Candidate of Engineering., Assoc. Prof.; ResearcherID: A-2772-2014,ORCID: https://orcid.org/0000-0002-0469-2601
Victor V. Glukhikh, Doctor of Engineering, Prof.; ResearcherID: A-2418-2014, ORCID: https://orcid.org/0000-0001-6120-1867
Kristina A. Usova, Research Engineer; ResearcherID: GOJ-9248-2022, ORCID: https://orcid.org/0000-0002-6237-955X
Denis D. Chirkov, Research Engineer; ResearcherID: GOJ-9173-2022, ORCID: https://orcid.org/0000-0002-8027-1753
Pavel S. Zakharov, Postgraduate Student; ResearcherID: GOJ-9111-2022, ORCID: https://orcid.org/0000-0003-4016-2269
Alesya V. Vurasko, Doctor of Engineering, Prof.; ResearcherID: AAC-5594-2021, ORCID: https://orcid.org/0000-0002-9471-085X
Affiliation
Urals State Forest Engineering University, ul. Sibirsky Trakt, 37, Yekaterinburg, 620100, Russian Federation; shkuroae@m.usfeu.ru*, gluhihvv@m.usfeu.ru, usovaka@m.usfeu.ru, chirkovdd@m.usfeu.ru, zaharovps@m.usfeu.ru, vurasko2010@yandex.ru
Keywordscomposites, cellulose acetates, wood flour, acetate film waste, properties, experimental-statistical models of properties
For citation
Shkuro A.E., Glukhikh V.V., Usova K.A., Chirkov D.D., Zakharov P.S., Vurasko A.V. Deriving Biocomposites of Polymer Phase Plasticised Cellulose Acetates with Varying Degrees of Acetylation. Lesnoy Zhurnal = Russian Forestry Journal, 2023, no. 4, pp. 155–168. (In Russ.). https://doi.org/10.37482/0536-1036-2023-4-155-168
References
-
Biodegradable Polymer Blends and Composites from Renewable Sources. Ed. by Yu. Long. Translated from English. Saint Petersburg, Nauchnyye osnovy i tekhnologii Publ., 2013. 464 p. (In Russ.).
-
Gotlib E.M., Golovanova K.V., Selekhova A.A. Ways of Creating Biodegradable Polymeric Materials and Their Production Based on Plasticised Cellulose Diacetates. Kazan, KNRTU Publ., 2011. 132 p. (In Russ.).
-
Olkhov A.A., Khvatov A.V., Popov A.A., Zaikov G.E., Abzaldinov Kh.S. Technological Properties of Biodegradable Materials Based on Cellulose Diacetate and Soya Flour. Vestnik tekhnologicheskogo universiteta = Bulletin of the Kazan Technological University, 2016, vol. 19, no. 1, pp. 75–79. (In Russ.).
-
Casarano R., Fidale L.C., Lucheti C.M., Heinze T., Seoud O.A. Expedient, Accurate Methods for the Determination of the Degree of Substitution of Cellulose Carboxylic Esters: Application of UV–Vis Spectroscopy (Dye Solvatochromism) and FTIR. Carbohydrate Polymers, 2011, vol. 83, no. 3, pp. 1285–1292. https://doi.org/10.1016/j.carbpol.2010.09.035
-
De Freitas R.R., Senna A.M., Botaro V.R. Influence of Degree of Substitution on Thermal Dynamic Mechanical and Physicochemical Properties of Cellulose Acetate. Industrial Crops and Products, 2017, vol. 109, pp. 452–458. https://doi.org/10.1016/j.indcrop.2017.08.062
-
Del Gaudio I., Hunter-Sellars E., Parkin I.P. Williams D., Da Ros S., Curran K. Water Sorption and Diffusion in Cellulose Acetate: The Effect of Plasticisers. Carbohydrate Polymers, 2021, vol. 267, art. no. 118185. https://doi.org/10.1016/j.carbpol.2021.118185
-
Feng J., Li S., Peng R., Sun T., Xie X., Shi Q. Effects of Fungal Decay on Properties of Mechanical, Chemical, and Water Absorption of Wood Plastic Composites. Journal of Applied Polymer Science, 2021, vol. 138, no. 11, art. no. 50022. https://doi.org/10.1002/app.50022
-
Ghareeb H.O., Radke W. Characterization of Cellulose Acetates According to DS and Molar Mass Using Two-Dimensional Chromatography. Carbohydrate Polymers, 2013, vol. 98, no. 2, pp. 1430–1437. https://doi.org/10.1016/j.carbpol.2013.07.061
-
Kono H., Hashimoto H., Shimizu Y. NMR Characterization of Cellulose Acetate: Chemical Shift Assignments, Substituent Effects, and Chemical Shift Additivity. Carbohydrate Polymers, 2015, vol. 118, pp. 91–100. https://doi.org/10.1016/j.carbpol.2014.11.004
-
Krishnamachari P., Hashaikeh R., Tiner M. Modified Cellulose Morphologies and Its Composites; SEM and TEM Analysis. Micron, 2011, vol. 42, no. 8, pp. 751–761. https://doi.org/10.1016/j.micron.2011.05.001
-
Polman E.M.N., Gruter G.M., Parsons J.R., Tietema A. Comparison of the Aerobic Biodegradation of Biopolymers and the Corresponding Bioplastics: A Review. The Science of the Total Environment, 2021, vol. 753, art. no. 141953. https://doi.org/10.1016/j.scitotenv.2020.141953
-
Rodriguez L.J., Peças P., Carvalho H., Orrego C.E. A Literature Review on Life Cycle Tools Fostering Holistic Sustainability Assessment: An Application in Biocomposite Materials. Journal of Environmental Management, 2020, vol. 262, art. no. 110308. https://doi.org/10.1016/j.jenvman.2020.110308
-
Samios E., Dart R.K., Dawkins J.V. Preparation, Characterization and Biodegradation Studies on Cellulose Acetates with Varying Degrees of Substitution. Polymer, 1997, vol. 38, no. 12, pp. 3045–3054. https://doi.org/10.1016/S0032-3861(96)00868-3
-
Senna A.M., Botaro V.R. Biodegradable Hydrogel Derived from Cellulose Acetate and EDTA as a Reduction Substrate of Leaching NPK Compound Fertilizer and Water Retention in Soil. Journal of Controlled Release: Official Journal of the Controlled Release Society, 2017, vol. 260, pp. 194–201. https://doi.org/10.1016/j.jconrel.2017.06.009
-
Senna A.M., Menezes A.J., Botaro V.R. Estudo Da Densidade de Ligações Cruzadas Em Géis Superabsorventes Obtidos Do Acetato de Celulose. Polímeros, 2012, vol. 23, no. 1, pp. 59–64. https://doi.org/10.1590/S0104-14282012005000078
-
Suvorova A.I., Demchik L.Y., Peshekhonova A.L., Sdobnikova O.A. Chemical Structure of Plasticizers, Compatibility of Components and Phase Equilibrium in Plasticized Cellulose Diacetate. Die Makromolekulare Chemie, 1993, vol. 194, no. 5, pp. 1315–1321. https://doi.org/10.1002/macp.1993.021940506
-
Takatani M., Ikeda K., Sakamoto K., Okamoto T. Cellulose Esters as Compatibilizers in Wood / Poly (Lactic Acid) Composite. Journal of Wood Science, 2008, vol. 54, no. 1, pp. 54–61. https://doi.org/10.1007/s10086-007-0911-y
-
Vandermeulen G.W., Boarino A., Klok H.A. Biodegradation of Water‐Soluble and Water‐Dispersible Polymers for Agricultural, Consumer, and Industrial Applications–Challenges and Opportunities for Sustainable Materials Solutions. Journal of Polymer Science, 2022, vol. 60, no. 12, pp. 1797–1813. https://doi.org/10.1002/pol.20210922
-
Watanabe S., Takai M., Hayashi J. An X-Ray Study of Cellulose Triacetate. Journal of Polymer Science Part C Polymer Symposia, 2007, vol. 23, no. 2, pp. 825–835. https://doi.org/10.1002/polc.5070230238
-
Vinod A., Sanjay M.R., Suchart S., Jyotishkumar P. Renewable and Sustainable Biobased Materials: An Assessment on Biofibers, Biofilms, Biopolymers and Biocomposites. Journal of Cleaner Production, 2020, vol. 258, art. no. 120978. https://doi.org/10.1016/j.jclepro.2020.120978
-
Yadav N., Hakkarainen M. Degradable or Not? Cellulose Acetate as a Model for Complicated Interplay Between Structure, Environment and Degradation. Chemosphere, 2021, vol. 265, art. no. 128731. https://doi.org/10.1016/j.chemosphere.2020.128731
|
Make a Submission
Lesnoy Zhurnal (Russian Forestry Journal) was awarded the "Seal of Recognition for Active Data Provider of the Year 2024"
|