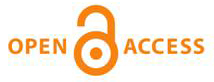
Address: Naberezhnaya Severnoy Dviny, 17, Arkhangelsk, 163002, Russian Federation, Northern (Arctic) Federal University named after M.V.Lomonosov, office 1425
Phone: +7 (8182) 21-61-18
E-mail: forest@narfu.ru
http://lesnoizhurnal.ru/en/
|
Features of Changing Structural and Morphological Properties of Bamboo Pulp During Refining. P. 146–159
|
 |
Hoang M. Khoa, Yakov V. Kazakov, Elena O. Okulova
UDС
676.16.022.6.034
DOI:
10.37482/0536-1036-2023-2-146-159
Abstract
The wood of tropical plants, including bamboo, has great potential due to its rapid growth, simple cultivation, low cost, and characteristics suitable for the pulp and paper industry. The study considers the structural-morphological properties of unbleached kraft pulp from the wood of Bambusa blumeana, which grows in the Republic of Vietnam. Kraft cooking was carried out on an autoclave system, CAS 420. The obtained bamboo pulp had a yield of 41.7 %, the Kappa number was 17.3. Structural and morphological properties are determined by an automatic fiber analyzer, L&W Fiber Tester. Digital microphotographs were taken with an ImagerM2m Carl Zeiss microscope. Samples were studied before and after refining at the Yokro mill up to 60 °SR. A comparison of the change in the structural and dimensional properties of bamboo pulp fibers was made with industrial softwood and hardwood unbleached pulp. It has been established that, with a general, similar to hardwood and softwood pulp, the nature of the change in properties during refining – a decrease in the average fiber length (from 1.90 up to 1.21 mm), an increase in width (from 17.8 to 20.6 μm), shape factor (from 81.7 to 85.6 %), fines content (from 1.8 to 7.0 %), a decrease in the number of kinks per fiber (from 0,78 to 0,72), the average segment length (from 1.17 to 0.86 mm), also observed for softwood and hardwood pulp, the change in the values of the structural and dimensional characteristics of the fibers in pulp from bamboo occurs to the greatest extent. The reduced fiber width with a high fiber length provides the highest values of the fiber slenderness ratio l/w (from 106.6 for unrefined to 58.8 at 60 °SR) in comparison with softwood (from 81.3 to 60.6) and especially hardwood (from 44.4 to 36.0), which in turn leads to a reduced shape factor and easier damage to the fibers under hydromechanical action during refining, which is expressed in a change in the number of kinks on a fiber. The maximum changes in the structure, size, shape of the fiber and fine content occur already in the first 10 minutes of refining, which indicates the low strength of bamboo fibers and their easy damage. Therefore, it can be assumed that the use of unbleached bamboo pulp in brown paper furnishing will not lead to an increase in its strength.
Keywordsbamboo pulp, papermaking properties, structural-morpholоgical propertes of pulp, refining, fiber length, fiber width, fractional composition
For citation
Khoa H.M., Kazakov Ya.V., Okulova E.O. Features of Changing Structural and Morphological Properties of Bamboo Pulp During Refining. Lesnoy Zhurnal = Russian Forestry Journal, 2023, no. 2, pp. 146–159. (In Russ.). https://doi.org/10.37482/0536-1036-2023-2-146-159
References
-
Beloglazov V.I., Komarov V.I., Dyakova E.V., Guryev A.V. Structural and Dimensional Properties of Semi-Finished Pulp Fibers as a Factor Determining Quality of Container Board Product. The Issues in Mechanics of Pulp and Paper Materials: Proceedings of the 1st International Scientific-Technical Conference. Arkhangelsk, September 13–17, 2011. Arkhangelsk, NArFU Publ., 2011, pp. 57–63. (In Russ.).
-
Guryev A.V., Dernov A.I., Dyakova E.V. Evaluation of Fiber’s Properties in Structured and Unstructured States. Part I. Semi-Finished Products for Container Board. Tsellyuloza. Bumaga. Karton = Pulp. Paper. Board, 2013, no. 1, pp. 67–70. (In Russ.).
-
Kazakov Ya.V. Characterization of Geometrical Parameters of Fibers of Cellulose Semi-Finished Products with the Use of Probabilistic Methods. Khimiya rastitel’nogo syr’ya = Chemistry of Plant Raw Material, 2014, no. 1, pp. 269–275. (In Russ.). https://doi.org/10.14258/jcprm.1401269
-
Kazakov Ya.V., Manakhova T.N. Paper-Forming Potential of Softwood Unbleached Pulp: The Modern View Using the Automatic Fiber Analyzer. Tsellyuloza. Bumaga. Karton = Pulp. Paper. Board, 2013, no. 5, pp. 34–39. (In Russ.).
-
Lebedev I.V. Simulation of Structure and Deformation Properties of Paper Sheet: Cand. Tech. Sci. Diss. Arkhangelsk, 2017. 150 p. (In Russ.).
-
Penkin A.A., Kazakov Ya.V. Changes in the Morphological Characteristics of Secondary Fiber Obtained from Wet-Strength Paper During Gentle Refining of Recycled Pulp. Part 1. Fiber Characteristics. Lesnoy Zhurnal = Russian Forestry Journal, 2022, no. 5, pp. 157–172. (In Russ.). https://doi.org/10.37482/0536-1036-2022-5-157-172
-
Aprianis Y., Novriyanti E., Akbar O.T. The Characteristics of Thorny Bamboo (Bambusa blumeana) for Dissolving Pulp. IOP Conference Series: Earth and Environmental Science, 2020, vol. 415, no. 1, p. 012024. https://doi.org/10.1088/1755-1315/415/1/012024
-
Chen Z., Zhang H., He Z., Zhang L., Yue X. Bamboo as an Emerging Resource for Worldwide Pulping and Papermaking. Bioresources, 2018, vol. 14, no. 1, pp. 3–5. https://doi.org/10.15376/biores.14.1.3-5
-
Draft Strategy for the Development of Forestry in Vietnam for the Period 2006–2020. Vietnam Administration of Forestry. (In Vietnamese). Available at: https://tongcuclamnghiep.gov.vn/LamNghiep/Index/chien-luoc-phat-trien-lam-nghiep-viet-nam-giai-doan-2006-2020-626 (accessed 25.03.23).
-
Ferdous T., Quaiyyum M.A., Bashar S., Jahan M.S. Anatomical, Morphological and Chemical Characteristics of Kaun Straw (Seetaria-Ltalika). Nordic Pulp & Paper Research Journal, 2020, vol. 35, no. 2, pp. 288–298. https://doi.org/10.1515/npprj-2019-0057
-
Gharehkhani S., Sadeghinezhad E., Kazi S.N., Yarmand H., Badarudin A., Safaei M.R., Zubir M.N.M. Basic Effects of Pulp Refining on Fiber Properties: A Review. Carbohydrate Polymers, 2015, vol. 115, pp. 785–803. http://dx.doi.org/10.1016/j.carbpol.2014.08.047
-
Hagaev O., Zou X. A New Concept to Characterize Fiber Development in Refining and Mechanical Pulp Quality for LWC and SC Grades. Pulp and Paper, Canada, Ontario, 2007, vol. 108, pp. 50–56.
-
Haiyan Ni, Yonggui Li, Shiwei Fu. Morphological Structure and Properties of Bamboo Shell Fiber. Journal of Natural Fibers, 2018, vol. 15, no. 4, pp. 586–595. https://doi.org/10.1080/15440478.2017.1349710
-
Kamthai S., Puthson P. The Physical Properties, Fiber Morphology and Chemical Compositions of Sweet Bamboo (Dendrocalamus asper Backer). Natural Science, 2005, vol. 39, pp. 581–587.
-
Karlsson H., Rinnevuo T. Fibre Guide: Fibre Analysis and Process Applications in the Pulp and Paper Industry. Sweden, Kista, AB Lorentzen and Wettre Publ., 2006. 120 p.
-
Lee K.-S., Song W.-Y., Shin S.-J. Elucidating Soda and Soda-Anthraquinone Pulping Characteristics of Korean Bamboo Species. Peolpeu Jong’i Gi’sul, 2016, vol. 48, no. 3, p. 44. https://doi.org/10.7584/ktappi.2016.48.3.044
-
Li B., Bandekar R., Zha Q., Alsaggaf A., Ni Y. Fiber Quality Analysis: OpTest Fiber Quality Analyzer versus L&W Fiber Tester. Industrial and Engineering Chemistry Research, 2011, vol. 50, no. 22, pp. 12572–12578. http://dx.doi.org/10.1021/ie201631q
-
Marja-Sisko, Ilvessalo-Pfäffli Leaf Fibers. Fiber Atlas: Identification of Papermaking Fibers. Springer Series in Wood Science. Ed. by T.E. Timell. Heidelberg, Springer-Verlag Berlin Publ., 1995. 400 p. https://doi.org/10.1007/978-3-662-07212-7
-
Mera F.A.T., Xu C. Plantation Management and Bamboo Resource Economics in China. Ciencia y Tecnología, 2014, vol. 7, no. 1, pp. 1–12. https://doi.org/10.18779/cyt.v7i1.93
-
Monga S., Thapliyal B.P., Tyagi S., Naithani S. Relationship between Strength Properties and Fiber Morphological Characteristics of S. Officinarum. International Journal of Science and Research, 2017, vol. 6, no. 1, pp. 1549–1556. https://doi.org/10.21275/ART20164484
-
Sharma A.K., Dutt D., Upadhyaya J.S., Roy T.K. Anatomical, Morphological, and Chemical Characterization of Bambusa tulda, Dendrocalamus hamiltonii, Bambusa balcooa, Malocana baccifera, Bambusa arundinacea, and Eucalyptus tereticornis. Bioresources, vol. 6, no. 4, pp. 5062-5073. http://dx.doi.org/10.15376/biores.6.4.5062-5073
-
Song B., Deng H., Tan L., Liu H. Fiber Structure and Basic Properties of Bamboo Pulp. Advanced Materials Research, 2011, vol. 332-334, pp. 874–877. https://doi.org/10.4028/www.scientific.net/AMR.332-334.874
-
Tripathi S.K., Mishra O.P., Bhardwaj N.K., Varadhan R. Pulp and Papermaking Properties of Bamboo Species Melocanna baccifera. Cellulose Chemical Technology, 2018, no. 52, pp. 81–88. Available at: https://www.cellulosechemtechnol.ro/pdf/CCT1-2(2018)/p.81-88.pdf
-
Wai N.N., Nanko H., Murakami K. A Morphological Study on the Behavior of Bamboo Pulp Fibers in the Beating Process. Wood Science and Technology, 1985, vol. 19, no. 3, pp. 211–222. https://doi.org/10.1007/BF00392050
|
Make a Submission
Lesnoy Zhurnal (Russian Forestry Journal) was awarded the "Seal of Recognition for Active Data Provider of the Year 2024"
|